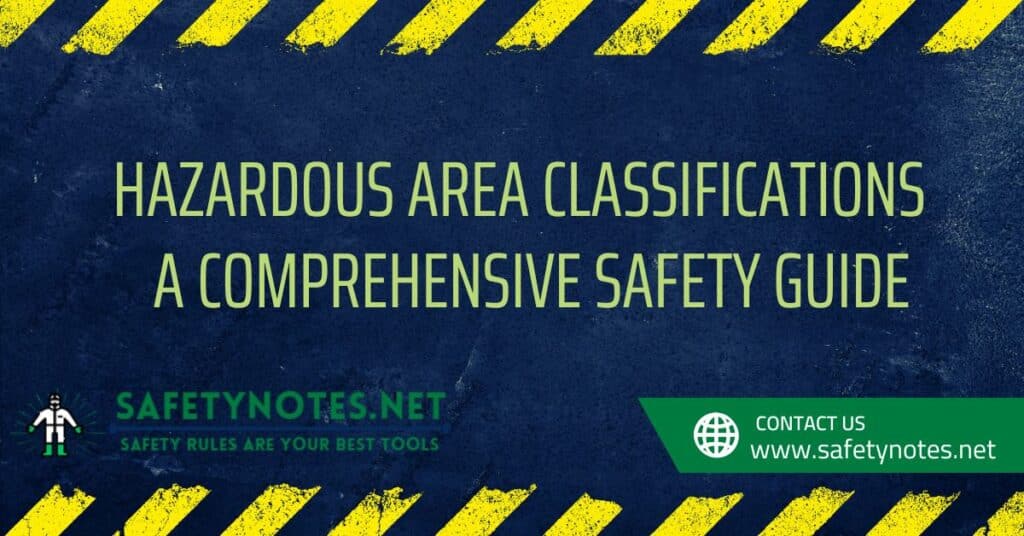
Introduction
In industrial settings, there are specific areas where the presence of flammable gases, vapors, combustible dusts, ignitable fibers, or flyings can lead to potential fire or explosion hazards. These areas are known as hazardous (or classified) locations, and it is crucial to understand the classifications and protection methods associated with them to ensure safety.
This comprehensive guide aims to provide a thorough understanding of hazardous area classifications and protections. We will explore the Class/Division system and the Zone system used for classification, along with various protection techniques. Additionally, we will discuss equipment protection level markings, temperature codes, approval agencies, and the responsibilities and precautions associated with hazardous areas.
Understanding Hazardous Areas
Definition and Risk of Explosive Atmospheres
Hazardous areas are locations where an explosive atmosphere, consisting of flammable gases, vapors, combustible dusts, ignitable fibers, or flyings, can occur. The presence of these hazardous materials poses a significant risk of fire or explosion, making it crucial to implement appropriate protective measures.
Class/Division System
The Class/Division system is primarily used in the United States and Canada to classify hazardous areas. It involves categorizing locations based on Class, Division, and Group.
Classifications in the Class/Division System
- Class I: Locations with flammable gases or vapors that may or may not be present in sufficient quantities to produce explosive or ignitable mixtures.
- Class I, Division 1: High probability of hazardous material presence continuously, intermittently, or periodically under normal operating conditions.
- Class I, Division 2: Low probability of hazardous material presence, occurring only during abnormal conditions for a short period.
- Class II: Locations with combustible dusts, which may or may not be present in sufficient quantities to produce explosive or ignitable mixtures.
- Class II, Division 1: High probability of hazardous material presence continuously, intermittently, or periodically under normal operating conditions.
- Class II, Division 2: Low probability of hazardous material presence, occurring only during abnormal conditions for a short period.
- Class III: Locations with ignitable fibers or flyings that may or may not be present in sufficient quantities to produce explosive or ignitable mixtures.
Zone System
The Zone system is used globally, except in the United States and Canada, for classifying hazardous areas. It categorizes locations based on Zones, which can be gas or dust atmospheres.
Classifications in the Zone System
- Gas Zones:
- Zone 0: Continuously present ignitable concentrations of flammable gases or vapors.
- Zone 1: Likely to have ignitable concentrations of flammable gases or vapors under normal operating conditions.
- Zone 2: Unlikely to have ignitable concentrations of flammable gases or vapors under normal operating conditions, occurring only for a short period.
- Dust Zones:
- Zone 20: Continuously present combustible dusts or ignitable fibers and flyings.
- Zone 21: Likely to have combustible dusts or ignitable fibers and flyings under normal operating conditions.
- Zone 22: Unlikely to have combustible dusts or ignitable fibers and flyings under normal operating conditions, occurring only for a short period.
Classification Systems
Classifications in the Class/Division System
The Class/Division system classifies hazardous locations based on three main criteria: Class, Division, and Group. These criteria help identify the nature and risk of the hazardous material present in the surrounding atmosphere.
Class
The Class defines the general nature or properties of the hazardous material in the atmosphere. There are three classes in the Class/Division system:
- Class I: Locations with flammable gases or vapors.
- Class II: Locations with combustible dusts.
- Class III: Locations with ignitable fibers or flyings.
Each class may or may not have the hazardous material in sufficient quantities to produce explosive or ignitable mixtures.
Division
The Division indicates the probability of the hazardous material being able to produce an explosive or ignitable mixture based on its presence. There are two divisions in the Class/Division system:
- Division 1: Indicates a high probability of hazardous material presence continuously, intermittently, or periodically under normal operating conditions.
- Division 2: Indicates a low probability of hazardous material presence, occurring only during abnormal conditions for a short period.
Group
The Group specifies the type of hazardous material in the surrounding atmosphere. For Class I locations (flammable gases or vapors), there are four groups:
- Group A: Atmospheres containing acetylene.
- Group B: Atmospheres containing flammable gases or vapors with low Maximum Experimental Safe Gap (MESG) or Minimum Igniting Current (MIC) ratio values.
- Typical gases: hydrogen, butadiene, ethylene oxide, propylene oxide, and acrolein.
- Group C: Atmospheres containing flammable gases or vapors with medium MESG or MIC ratio values.
- Typical gases: ethyl ether, ethylene, acetaldehyde, and cyclopropane.
- Group D: Atmospheres containing flammable gases or vapors with high MESG or MIC ratio values.
- Typical gases: acetone, ammonia, benzene, butane, ethanol, gasoline, methane, natural gas, naphtha, and propane.
For Class II and Class III locations (combustible dusts or ignitable fibers), there are three groups:
- Group E: Atmospheres containing combustible metal dusts, such as aluminum, magnesium, and their commercial alloys.
- Group F: Atmospheres containing combustible carbonaceous dusts with 8% or more trapped volatiles, such as carbon black, coal, or coke dust.
- Group G: Atmospheres containing combustible dusts not included in Group E or Group F.
- Typical dusts: flour, starch, grain, wood, plastic, and chemicals.
Classifications in the Zone System
The Zone system classifies hazardous areas based on Zones, which can be gas or dust atmospheres. Each zone represents the probability of the hazardous material being present in sufficient quantities to produce explosive or ignitable mixtures.
Gas Zones
- Zone 0: Locations with continuously present ignitable concentrations of flammable gases or vapors.
- Zone 1: Locations likely to have ignitable concentrations of flammable gases or vapors under normal operating conditions.
- Zone 2: Locations unlikely to have ignitable concentrations of flammable gases or vapors under normal operating conditions, occurring only for a short period.
Dust Zones
- Zone 20: Locations with continuously present combustible dusts or ignitable fibers and flyings.
- Zone 21: Locations likely to have combustible dusts or ignitable fibers and flyings under normal operating conditions.
- Zone 22: Locations unlikely to have combustible dusts or ignitable fibers and flyings under normal operating conditions, occurring only for a short period.
Protection Techniques and Methods
Various protection techniques and methods are employed to reduce or minimize the potential risks of explosion or fire from electrical equipment in hazardous locations. These techniques ensure the safety of personnel and equipment operating in these environments.
Explosion-Proof Protection
Explosion-proof protection is a type of protection that involves using an enclosure capable of withstanding an explosive gas or vapor within it. The enclosure also prevents the ignition of an explosive gas or vapor surrounding it. This type of protection operates at an external temperature that ensures the surrounding explosive atmosphere will not be ignited.
Intrinsically Safe Protection
Intrinsically safe protection ensures that electrical equipment, under normal or abnormal conditions, is incapable of releasing sufficient electrical or thermal energy to cause ignition of a specific hazardous atmospheric mixture in its most easily ignitable concentration.
Dust Ignition-Proof Protection
Dust ignition-proof protection ensures that electrical equipment excludes ignitable amounts of dust or amounts that might affect its performance or rating. When installed and protected in accordance with the original design intent, this protection prevents arcs, sparks, or heat generated inside the enclosure from causing ignition of exterior accumulations or atmospheric suspensions of specified dust.
Non-Incendive Protection
Non-incendive protection involves electrical equipment that, under normal conditions, cannot cause ignition of a specified flammable gas or vapor-in-air mixture due to arcing or thermal effects.
Type n Protection
Type n protection applies to electrical equipment that, in normal operation, is not capable of igniting a surrounding explosive atmosphere.
Type t Protection
Type t protection involves electrical equipment equipped with an enclosure providing dust ingress protection and a means to limit surface temperatures.
Type h Protection
Type h protection refers to three different types of protection:
- Constructional measures to protect against the possibility of ignition from hot surfaces, sparks, and compression generated by moving parts.
- Ignition protection using mechanical or electrical devices in conjunction with nonelectrical equipment to reduce the likelihood of a potential ignition source becoming effective.
- Protection where potential ignition sources are made ineffective or separated from the explosive atmosphere by immersing them in a protective liquid.
Equipment Protection Level (EPL) Markings
Equipment Protection Level (EPL) markings indicate the level of protection given to equipment based on the likelihood of it becoming a source of ignition. EPL markings differentiate between explosive gas atmospheres, explosive dust atmospheres, and explosive atmospheres in mines susceptible to firedamp.
Temperature Code (T Code)
The temperature code, represented as a T Code, determines the maximum surface temperature that a product will not exceed under specified ambient temperatures. This information is vital to prevent the ignition of hazardous gases or dusts due to contact with hot surfaces.
Nomenclature and Approval Markings
Different approval markings are used to indicate the suitability of equipment for hazardous areas. These markings help users identify the appropriate equipment for their specific hazardous location.
Class/Division System Approval Markings
Equipment approved under the Class/Division system is marked with the following information:
- Class and Division: Indicates the specific class and division for which the equipment is approved (e.g., Class I, Division 2).
- Group: Specifies the group of hazardous material the equipment is designed for (e.g., Group C for flammable gases or vapors).
- Temperature Code (T Code): Indicates the maximum surface temperature the equipment will not exceed under specified ambient temperatures (e.g., T5).
- Additional Notation for Intrinsically Safe Equipment: For intrinsically safe equipment, the words “Intrinsically Safe” or “IS” precede the approval marking (e.g., IS CL I, II, III Div 1 GP ABCDEFG).
Zone System Approval Markings
Equipment approved under the Zone system is marked with the following information:
- Protection Concept: Indicates the specific type of protection used (e.g., “Ex d” for flame-proof protection).
- Zone: Specifies the zone in which the equipment can be safely used (e.g., Zone 1 for likely ignitable concentrations).
- Group: Identifies the group of hazardous material for which the equipment is designed (e.g., Group IIC for acetylene or hydrogen).
- Temperature Code (T Code): Indicates the maximum surface temperature the equipment will not exceed under specified ambient temperatures (e.g., T6).
Hazardous Area Precautions and Responsibilities
Operating in hazardous areas requires strict adherence to safety precautions and responsibilities to ensure the safety of personnel and equipment. Here are some key precautions and responsibilities:
- Compliance with Classification: Determine the hazardous area classification and ensure that only approved equipment suitable for that classification is used.
- Training and Awareness: Provide comprehensive training and awareness programs for personnel working in hazardous areas to recognize potential risks and apply safety procedures.
- Preventing Ignition Sources: Implement measures to prevent potential ignition sources, such as sparks, arcs, and hot surfaces, from coming into contact with flammable gases, vapors, or combustible dusts.
- Maintenance and Inspection: Regularly inspect and maintain equipment to ensure it remains in good working condition and continues to meet safety standards.
- Proper Ventilation: Maintain adequate ventilation in hazardous areas to disperse hazardous gases or dust concentrations.
- Personal Protective Equipment (PPE): Provide appropriate PPE to personnel working in hazardous areas to protect them from potential hazards.
- Emergency Response Plan: Develop and implement an emergency response plan to quickly and efficiently address any incidents or potential hazards in hazardous areas.
- Permit-to-Work System: Implement a permit-to-work system to control and monitor activities in hazardous areas, ensuring that only authorized personnel with proper training and qualifications perform work in such areas.
Regulatory Compliance and Standards
Hazardous area classifications and protections are governed by various regulations and standards to ensure uniformity and safety. Compliance with these regulations and standards is essential to prevent accidents and ensure the safe operation of equipment in hazardous locations.
National and International Standards
Several national and international standards govern hazardous area classifications and protections. Some of the key standards include:
- NFPA 70: National Electrical Code (NEC): The NEC provides requirements for electrical installations, including those in hazardous locations, in the United States.
- CSA C22.1: Canadian Electrical Code (CE Code): The CE Code sets safety standards for electrical installations, including those in hazardous locations, in Canada.
- IEC 60079: Explosive Atmospheres Series: This series of standards, developed by the International Electrotechnical Commission (IEC), covers equipment and protection methods for explosive atmospheres.
Industry-Specific Standards
In addition to national and international standards, certain industries have specific standards tailored to their needs. For example:
- API RP 500 and API RP 505: These standards, issued by the American Petroleum Institute (API), provide guidelines for electrical equipment in hazardous locations in the petroleum industry.
- IECEx Scheme: International Electrotechnical Commission Scheme for Certification to Standards Relating to Equipment for Use in Explosive Atmospheres: This scheme ensures that equipment used in hazardous areas meets international safety requirements.
Conclusion
Understanding hazardous area classifications and protections is crucial to ensuring the safety of personnel and equipment in industrial settings. The Class/Division system and the Zone system are the two main classification systems used globally. Various protection techniques, such as explosion-proof, intrinsically safe, and dust ignition-proof protection, safeguard electrical equipment in hazardous areas.
Equipment protection level markings, temperature codes, and approval markings aid in identifying suitable equipment for specific hazardous locations. Compliance with regulatory standards and safety precautions is essential to prevent accidents and maintain a safe working environment.
By following the guidelines, regulations, and standards, industries can minimize the risks associated with hazardous areas and create a safer and more secure workplace for all personnel involved.
Frequently Asked Questions (FAQs) – Hazardous Area Classifications and Protections
1. What are hazardous areas, and why is it important to understand their classifications and protections?
Hazardous areas are locations where explosive atmospheres, consisting of flammable gases, vapors, combustible dusts, ignitable fibers, or flyings, can occur, posing a risk of fire or explosion. Understanding their classifications and protections is vital to ensure the safety of personnel and equipment operating in such environments.
2. What is the Class/Division system, and where is it primarily used?
The Class/Division system is primarily used in the United States and Canada to classify hazardous areas. It involves categorizing locations based on Class (e.g., Class I, II, III), Division (e.g., Division 1, Division 2), and Group (e.g., Group A, B, C, D, E, F, G).
3. What are the Classifications under the Class/Division system?
- Class I: Locations with flammable gases or vapors.
- Class II: Locations with combustible dusts.
- Class III: Locations with ignitable fibers or flyings.
4. What does Class I, Division 1 signify in the Class/Division system?
Class I, Division 1 indicates a high probability of hazardous material presence continuously, intermittently, or periodically under normal operating conditions.
5. How does the Zone system differ from the Class/Division system in hazardous area classification?
The Zone system is used globally, except in the United States and Canada, and classifies hazardous areas based on Zones, which can be gas or dust atmospheres.
6. What are the Gas Zones in the Zone system?
- Zone 0: Locations with continuously present ignitable concentrations of flammable gases or vapors.
- Zone 1: Locations likely to have ignitable concentrations of flammable gases or vapors under normal operating conditions.
- Zone 2: Locations unlikely to have ignitable concentrations of flammable gases or vapors under normal operating conditions, occurring only for a short period.
7. What are the Dust Zones in the Zone system?
- Zone 20: Locations with continuously present combustible dusts or ignitable fibers and flyings.
- Zone 21: Locations likely to have combustible dusts or ignitable fibers and flyings under normal operating conditions.
- Zone 22: Locations unlikely to have combustible dusts or ignitable fibers and flyings under normal operating conditions, occurring only for a short period.
8. What are the three main criteria used to classify hazardous locations under the Class/Division system?
The three main criteria are Class, Division, and Group, which help identify the nature and risk of the hazardous material present in the atmosphere.
9. What does “Intrinsically Safe Protection” mean?
Intrinsically safe protection ensures that electrical equipment, under normal or abnormal conditions, is incapable of releasing sufficient electrical or thermal energy to cause ignition of a specific hazardous atmospheric mixture in its most easily ignitable concentration.
10. How does “Explosion-Proof Protection” work?
Explosion-proof protection involves using an enclosure capable of withstanding an explosive gas or vapor within it and preventing the ignition of the surrounding explosive atmosphere. This protection operates at an external temperature that ensures no ignition will occur.
11. What do the Equipment Protection Level (EPL) markings indicate?
Equipment Protection Level (EPL) markings indicate the level of protection given to equipment based on the likelihood of it becoming a source of ignition in explosive gas or dust atmospheres.
12. How is equipment approved for hazardous locations?
Equipment intended for hazardous locations must be approved by recognized approval agencies, such as Factory Mutual (FM) and Underwriters Laboratories (UL) in North America, and Ex Certification Bodies (ExCBs) in countries participating in the IECEx Scheme.
13. What precautions should be taken in hazardous areas?
Precautions include compliance with classifications, training and awareness programs, prevention of ignition sources, regular maintenance and inspection, proper ventilation, use of appropriate Personal Protective Equipment (PPE), and implementation of an emergency response plan and permit-to-work system.
14. What are the main national and international standards governing hazardous area classifications and protections?
The main standards include NFPA 70 (NEC) and CSA C22.1 (CE Code) for North America, IEC 60079 for international equipment, and industry-specific standards such as API RP 500 and API RP 505 for the petroleum industry.
15. Why is regulatory compliance crucial for hazardous area operations?
Regulatory compliance ensures uniformity and safety, preventing accidents and maintaining a safe working environment in hazardous locations.
Your very own commitment to getting the message throughout came to be rather powerful and have consistently enabled employees just like me to arrive at their desired goals.
safety training in chennai
And indeed, I’m just always astounded concerning the remarkable things served by you. Some four facts on this page are undeniably the most effective I’ve had.
offshore safety course in chennai
I have read your blog and I gathered some needful information from your blog. Keep update your blog. Waiting for your next update.
safety course in chennai
I love the information you provide here and can’t wait to take a look when I get home. I’m surprised at how fast your blog loaded on my cell phone. I’m not even using WIFI, just 3G. Anyways, awesome blog!
nebosh igc course in chennai
I love your blog.. very nice colors & theme.
Did you make this website yourself or did you hire someone to do it for you?
Plz answer back as I’m looking to create my own blog and would like to know where
u got this from. thanks
A person essentially assist to make significantly posts I would state.
That is the first time I frequented your website page and so far?
I surprised with the research you made to create this particular post amazing.
Excellent process!